

If you wanted to make 110 inch TVs, you could make two of them at a time. The Hefei Gen 10.5 fab is designed to produce the panels for either eight 65 inch or six 75 inch TVs on a single mother glass. The sheets of glass are only 0.5 - 0.7 mm thick or sometimes even thinner, so as you can imagine they are extremely fragile and can really only be handled by robots. The first modern LCD Fabs built in the early 1990s made sheets the size of a single notebook computer screen, and the size grew over time. The sandwich is next covered with special sheets of polarizing film, and the sheets are cut into individual “panels” – a term that is used to describe the subassembly that actually goes into a TV.įor the sake of efficiency, you would like to make as many panels on a sheet as possible, within the practical limitations of how big a sheet you can handle at a time. You have to align the two sheets so the colored dots sit right on top of the cells, and you can’t be off by more than a few microns in each direction anywhere on the sheet. Then you drop tiny amounts of liquid crystal material into the cells on the first sheet and glue the two sheets together. This is how you produce the colors when you shine light through it. On the other sheet of glass, you make an array of millions of red, green, and blue dots in a black matrix, called a color filter array (CFA). Remember, the average human hair is 40 microns in diameter. Each step has to be precisely aligned to the previous one within a few microns. This patterning step is repeated to build up tiny little cells, one for each dot (known as a pixel) on the screen.
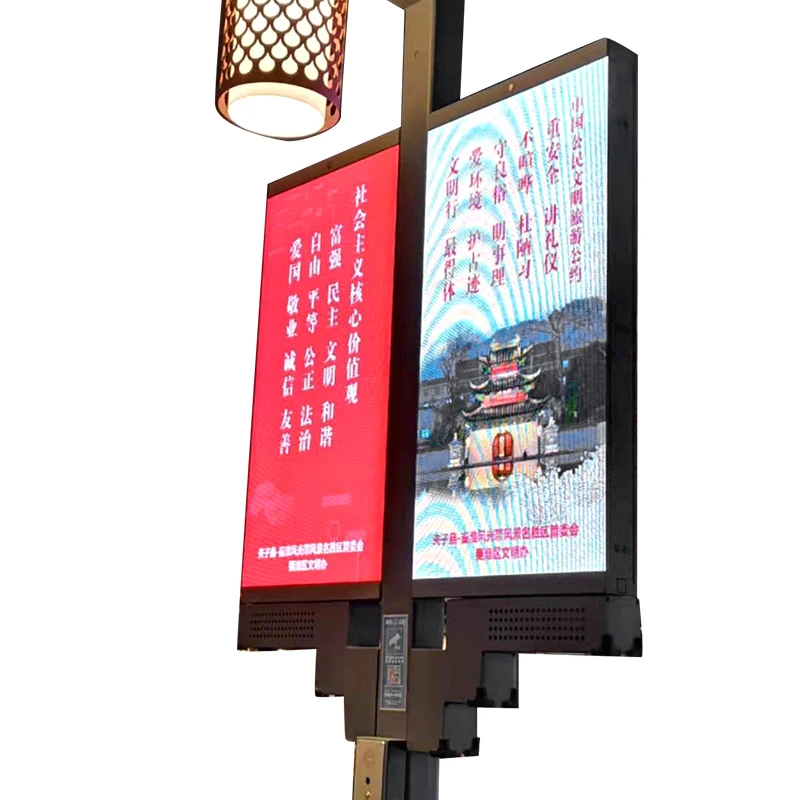
Then you deposit a layer of silicon, followed by a process that builds millions of precisely shaped transistor parts. That’s how you can get electrical signals to the middle of a screen. On one of the sheets are transistor “cells” formed by first depositing a layer of indium tin oxide (ITO), an unusual metal alloy that you can actually see through. Liquid crystal display (LCD) screens are manufactured by assembling a sandwich of two thin sheets of glass. BOE has a total of 12 fabs in Beijing, Chongqing, and several other major cities across China this particular factory was named Fab 9. This was the third factory, or “fab” that Beijing-based BOE built in Hefei alone, and in terms of capability, it is now the most advanced in the world.
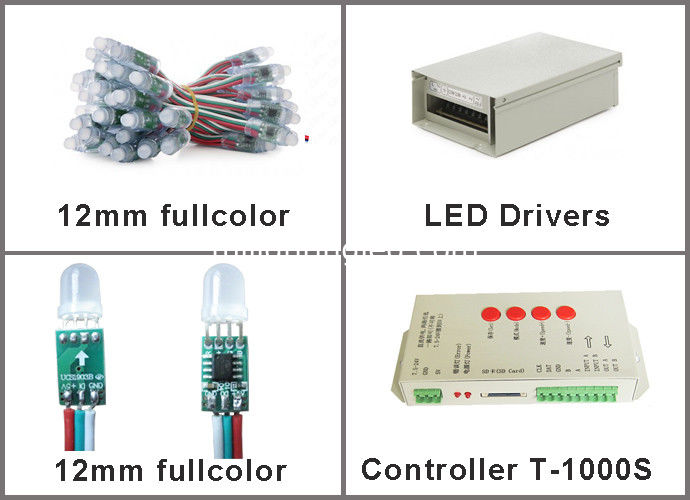
Last week I had the opportunity to tour BOE Technology Group’s Gen 10.5 factory in Hefei, the capital of China’s Anhui Province.
